Products

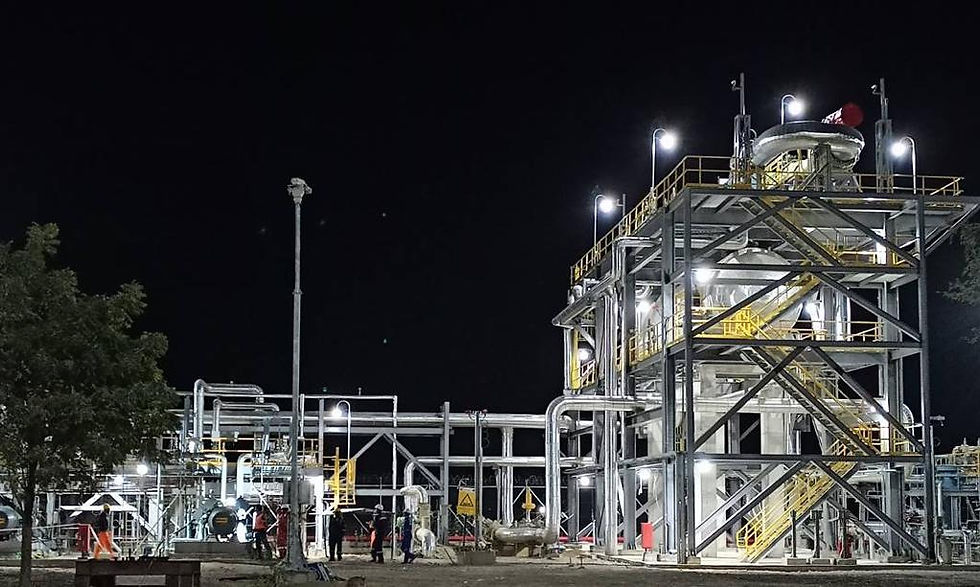


Separator
A cylindrical or spherical vessel used to separate oil, gas and water from the total fluid stream produced by a well. Separators can be either horizontal or vertical. Separators can be classified into two-phase and three-phase separators (commonly called free-water knockout). The two-phase type deals only with oil and gas, while the three-phase type handles oil, water and gas. Additionally, separators can be categorized according to their operating pressure. Low-pressure units handle pressures of 10 to 180 psi [69 to 1241 kPa]. Medium-pressure separators operate from 230 to 700 psi [1586 to 4826 kPa]. High-pressure units handle pressures of 975 to 1500 psi [6722 to 10,342 kPa]. Gravity segregation is the main force that accomplishes the separation, which means the heaviest fluid settles to the bottom and the lightest fluid rises to the top. Additionally, inside the vessel, the degree of separation between gas and liquid will depend on the separator operating pressure, the residence time of the fluid mixture and the type of flow of the fluid. Turbulent flow allows more bubbles to escape than laminar flow.
Indirect Bath Heater
Function: Indirect Bath heater increase the flow ability of the crude & breaks the emulsion so that it can be separated in separator as oil, gas & water by increasing the temperature of the crude oil.
Indirect bath heater also helps the heat the crude oil in storage tanks by circulating the hot water to tank with coil.
Design Code: API12K & ASME Sec VIII Div-1
Process Fluid: Crude Oil, Oil & Gas Mixture & Gas
Main Components: Shell, Flow coil, Fire Box, Burner system with management system & Expansion tank.
Burner Management system: Control the Liquid Level, Pressure & temperature of the Flow coil fluid, Temperature of the water, Pressure & temperature of the Fuel for the burner, Flame Failure detection, Exhaust temperature control, Air pressure control
Skid: Yes
Accessories: pressure, temperature, Flow & level control instruments, Fuel Gas Scrubber or filter, Hot water circulation skid
Insulation: Rockwool or Glasswool
0
1
2
3


Back Pressure Control valve
Back Pressure Valve can be used in any installation where upstream pressure is required to be kept at a preset range. It may also be used as: a pressure relief valve, a custody transfer dump valve to hold a certain back pressure, or as a separator back pressure valve on the gas or liquid side. Upstream pressure is applied to the bottom of the diaphragm through connecting tubing. Spring tension above the diaphragm opposes this pressure, and when the pressure exceeds the pressure setting on the spring, the plug is raised off the seat. By varying the spring tension, the pressure setting can be varied.
The typical application for these valves is to hold back pressure on separators, treaters, Lact units, etc.
Types of Back pressure Valves
3535 Diaphragm Operated Back Pressure Valve, Low Pressure
5555 Back Pressure Valve, Double Seated (Balanced)


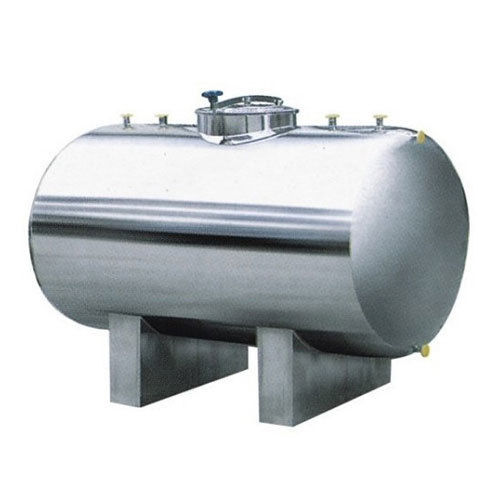


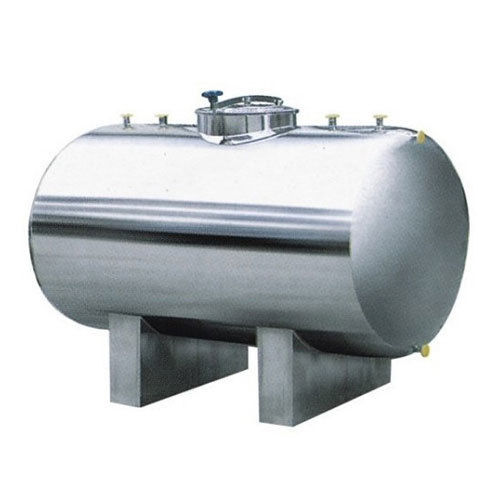
Horizontal Storage Tank
Design Standard: IS 10987 & Good Engineering practice
Types: Cylindrical & Corrugated Rectangular
Capacity: Up to 120 M3
Major MOC: IS 2062/ SA 516 Gr. 70 With inside Epoxy coating or Glass reinforced Vinyl Ester Paint.
Internal Coil: For Heating of the Stored liquid
Insulation: Rock wool or Glass Wool
Vessel Internal: Stilling Well, Heating coil, Guide control for the instruments, Vortex Breakers
Operation area: Monkey ladder With cage, Operator Platform, Dip hatch, Manhole
Safety & Instrumentation: Pressure Vaccum Relief Valve, Flame Arrestor with Goose neck vent, Level Transmitters, Pressure transmitters, Spray Sprinklers for Fire safety
Storage Tank
Petroleum industry requires storage tanks for holding crude oil prior to transportation to refineries. Storage tanks are available in many shapes: vertical and horizontal cylindrical; open top and closed top; flat bottom, cone bottom, slope bottom and dish bottom. S. Mark’s Large tanks tend to be vertical cylindrical, or to have rounded corners transition from vertical side wall to bottom profile, to easier withstand hydraulic hydrostatically induced pressure of contained liquid.
S. Mark manufactured tank capacity:
200 – 1000m3





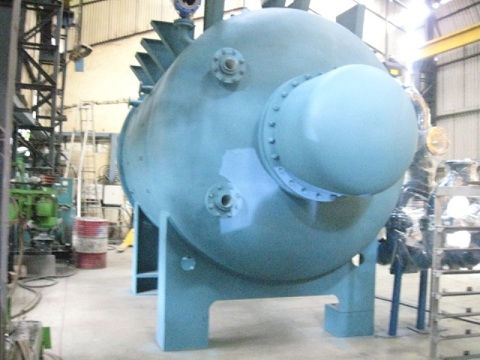
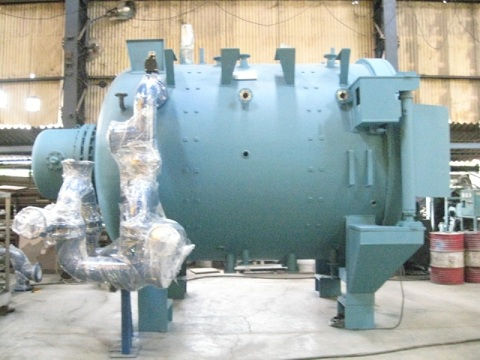

Vaccum Furnace
S. Mark has designed surge tanks used to store produced liquids before disposal. The tank can also be used as an additional stage of separation and metering. The design of the surge tank also makes it possible to use as a second stage, two phase separator with the addition of gas and fluid metering. The unit is very effective where a longer retention time is required for good separation of gas and fluids. Another advantage of the surge tank is that the design allows the operator to keep back pressure on transfer pumps for production disposal.
​
S. Mark Surge Tank Sizes:
-
Diameter: 1842mm
-
Length: 6000mm
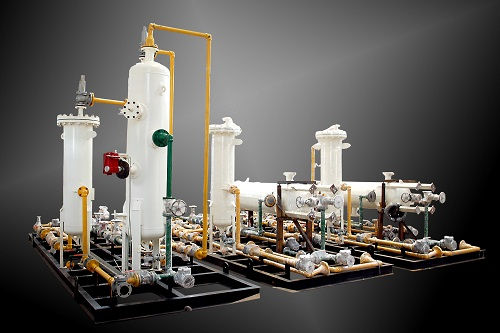
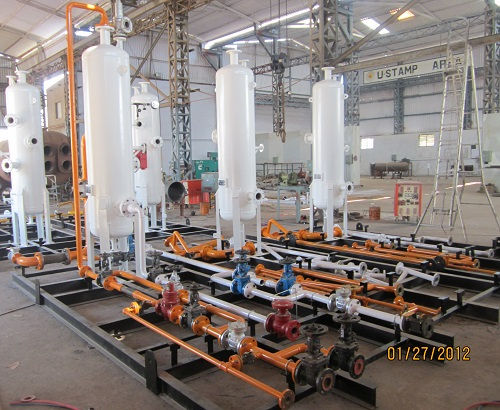
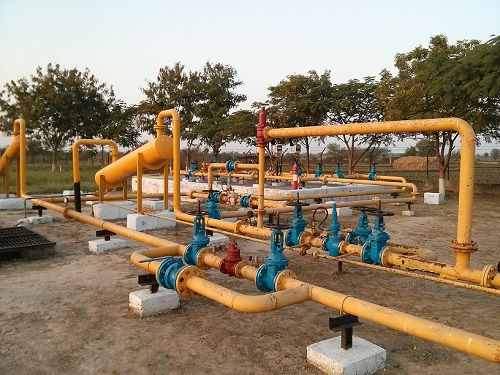
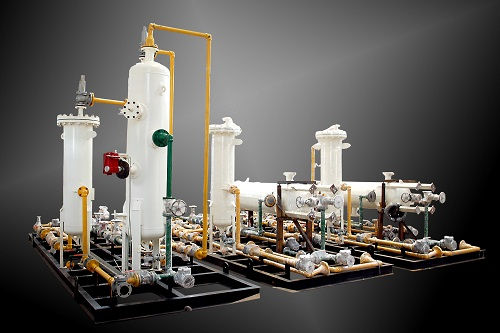
Gas Metering Skid
A gas metering skid is a part of a gas production plant that is pre-assembled on a steel structure, engaged to the measurement of gas products. It can be installed at the onshore or offshore location based on the requirement. Although several parameters are measured, the primary variable to be measured is the flow rate. Depending on the specific technology and user specifications, the measured flow rate can be a mass flow rate or a volumetric flow rate. The metering skid often used for further dealings, such as pressure-reduction by using control valves, filtration, and flow rate control by using different types of flow control valves.
Brine Filtration Unit
BRINCLEAN is S. Mark’s indigenously designed brine filtration unit. It meets industry requirements for good quality workover fluids.
​
BRINCLEAN is manufactured using high quality SS and strictly following ASME fabrication codes
​
BRINCLEAN produces brine with less than 4µ size
​
BRINCLEAN covers a wide range of filtering suspended particles: 40µ to 4µ sizes
​
BRINCLEAN has a 2 phase design that extends the life of the system




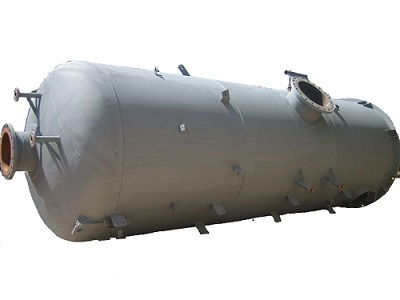

Knock Out Drums
Whenever a process requires that entrained droplets be removed from a vapor stream, a knockout drum should be integrated into the system. Condensation can occur when hot process gases cool considerably in the flare gas header and riser, and some gases also go to dew point at ambient temperatures and pressures and can therefore generate liquids. These droplets must be removed in order to avoid the phenomenon known as flaming rain, which occurs when liquid droplets are blown out the top of a flare stack along with ignited process gases. These vessels can be either horizontal or vertical.
​
S. Mark KOD Sizes:
​
-
Diameter: 3645mm
-
​
-
Length: 9144mm
Progressive Cavity Pump
S. Mark having significant experience in the field of Oil and Gas provides rental services for PCP (Progressive Cavity Pump) – ONGC Mehsana (100+ units)
These pumps need capital investment however taking on rental basis has been an optimum solution and cost effective in practice currently.
Client get benefit of our association with M/s. Altiris. M/s Altiris have world class manufacturing unit in Germany and Canada and well known for these pump to reputed client worldwide as Chevron, Total, Fuji, Petronas Etc.
At latest ONGC has been looking for such services and we are the prominent bidder for them.
Features :
-Installation friendly (Installing without rig)
-User friendly
-Easy to maintain and operate
-Cost effective
-Compact and concise
-
Client advantages
- Seamless services being S. Mark providing rental, operation, and repair services for cost effective solution regularly pan India.
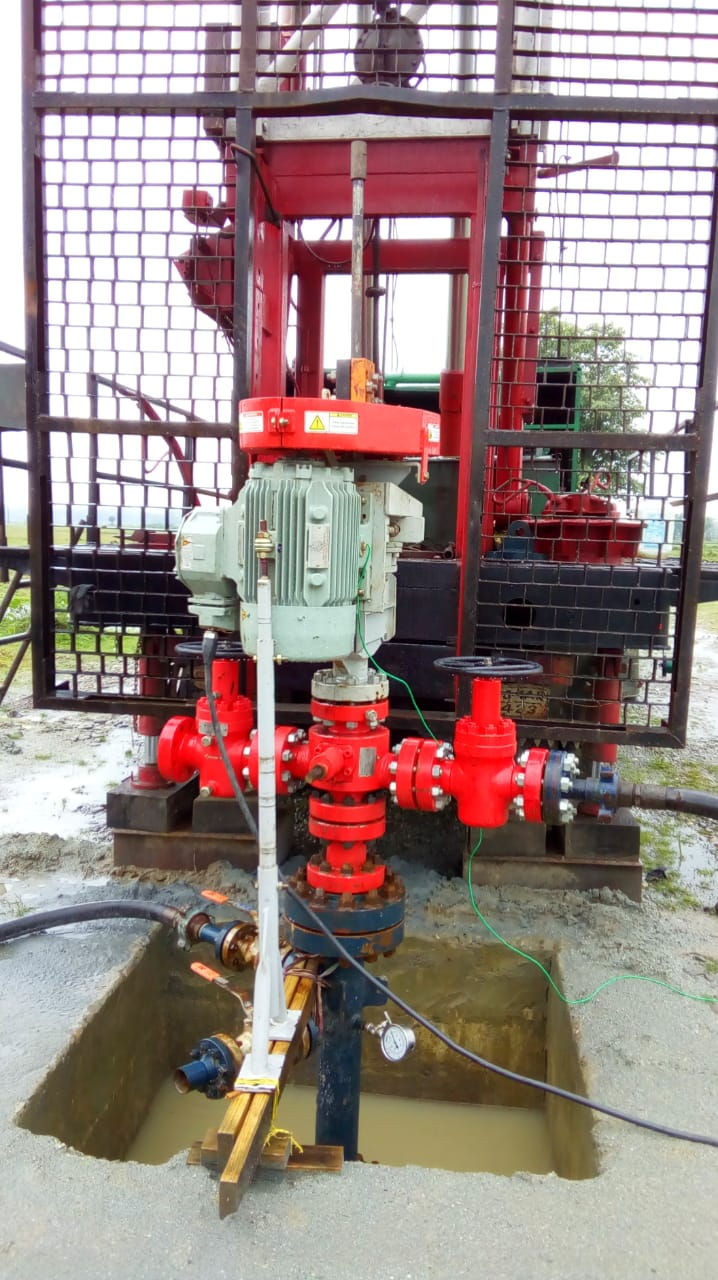
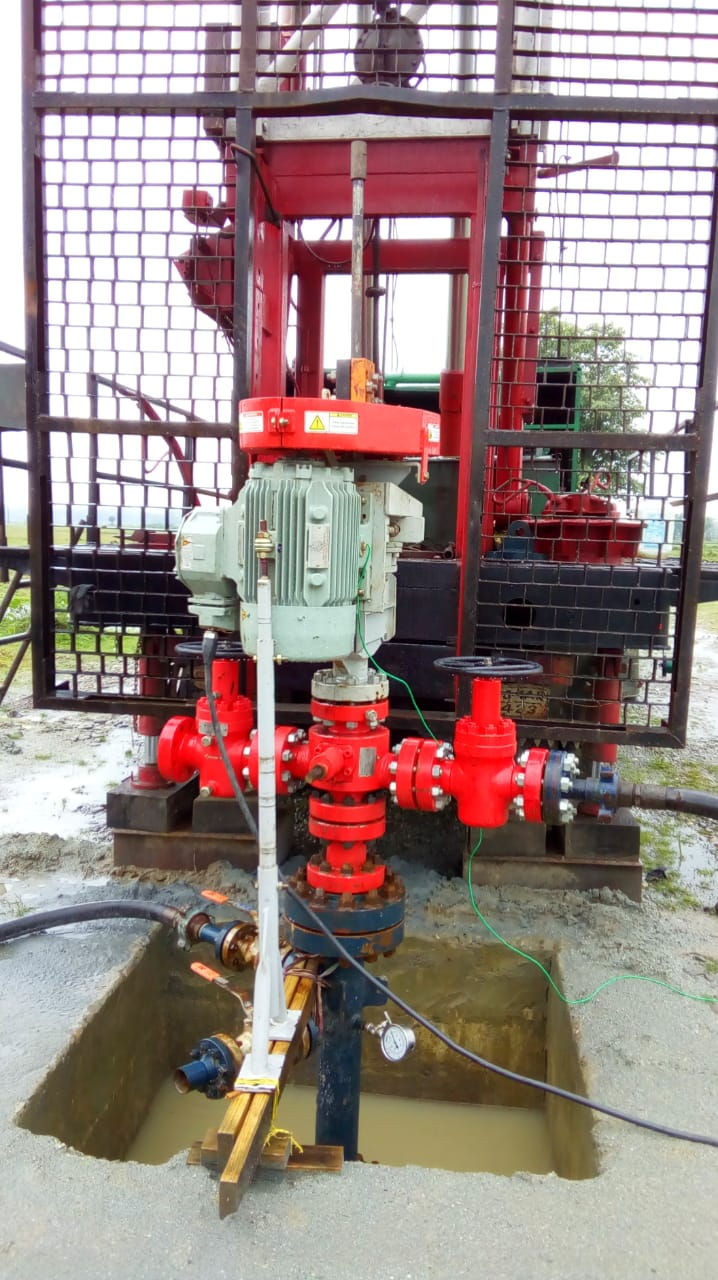